Data that makes ‘Sense’
Peter Haddock interviews Plinx founder Tommy Williams at Lynch’s Birmingham depot to find out how MachineSense is making a difference with its high quality data.
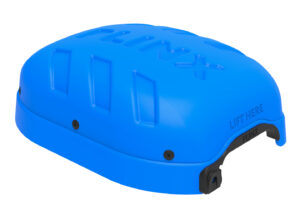
What is MachineSense?
With its quick installation to any machine, real-time data accessibility, and direct feedback to operators, MachineSense enables construction teams to take control and proactively address equipment-related inefficiencies, improve safety, maintain compliance and boost sustainability.
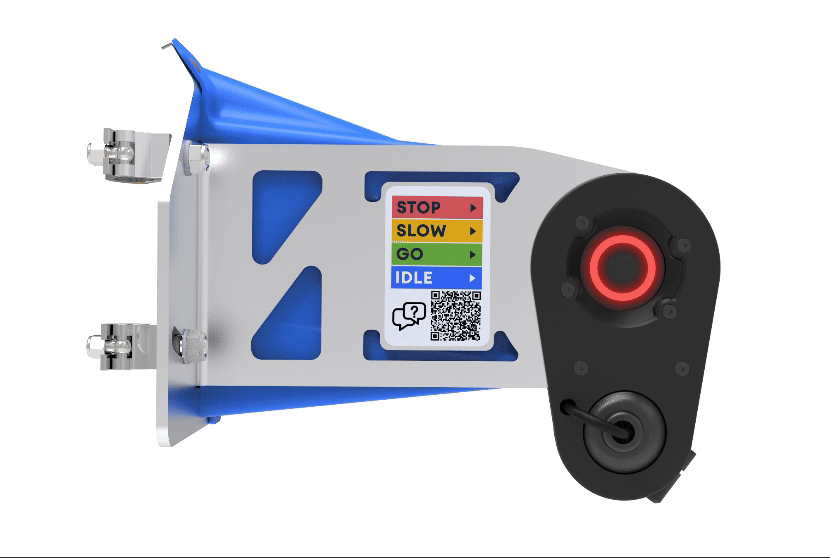
How does MachineSense make a difference
Immediate Feedback:
The operator interface is designed for real-time, on-site impact. It quickly attaches to the machine’s hand-rail or mirror bracket, providing proactive feedback through an LED ring. This ensures operators are immediately aware of any issues, while the integrated camera captures the driver’s eye view. This footage helps pinpoint the root causes of site ‘events,’ driving continuous improvement and encouraging responsible machine use.
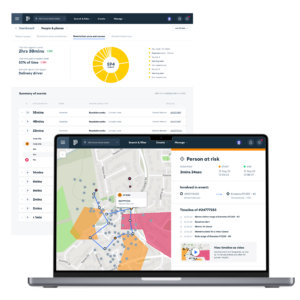
Data-Driven Decisions:
But how do you turn this feedback into actionable insights? That’s where our management platform comes in. The same data captured from the operator interface is instantly accessible through the Plinx platform, our API, one of our partner platforms, or a fully customisable Power BI solution. No matter the connection method, you’ll receive the same high-quality, actionable intelligence that enables smarter, data-driven decisions for both operators and managers.
MachineSense optimises equipment utilisation by tracking machine activity, identifying underutilised assets, and providing real-time insights on operational performance. This helps reduce idle time, ensures machines are used efficiently, and maximises productivity, leading to better resource management and cost savings.
MachineSense can be linked to the project plan, allowing contractors to track progress through cycle information (e.g., the number of times a machine has moved earth) or by the time spent within the ‘work area’
MachineSense helps identify the causes of unplanned downtime, whether it’s mechanical failure, missing labour, materials, or logistics issues such as traffic, providing valuable insights to avoid disruptions.
Rather than waiting for complaints, MachineSense’s in-cab display proactively alerts operators if they use machines outside of approved time windows or activate restricted functions, like vibratory rolling, ensuring compliance before issues arise.
MachineSense provides verifiable proof of task completion, such as dust suppression or road sweeping, helping to avoid hefty fines by ensuring that compliance requirements are met and documented in real-time.
MachineSense alerts operators when machines exceed site speed limits, helping to maintain safe operation and reduce the risk of accidents.
Ensure machines are only operated in authorised areas, reducing safety risks and improving site compliance with restricted access zones.
MachineSense minimises unnecessary idling, helping to lower fuel usage and reduce operational costs.
By preventing unconscious idling, MachineSense contributes to a cleaner, more sustainable operation, reducing carbon emissions on-site.
MachineSense optimises equipment utilisation by tracking machine activity, identifying underutilised assets, and providing real-time insights on operational performance. This helps reduce idle time, ensures machines are used efficiently, and maximises productivity, leading to better resource management and cost savings.
MachineSense can be linked to the project plan, allowing contractors to track progress through cycle information (e.g., the number of times a machine has moved earth) or by the time spent within the ‘work area’
MachineSense helps identify the causes of unplanned downtime, whether it’s mechanical failure, missing labour, materials, or logistics issues such as traffic, providing valuable insights to avoid disruptions.
Rather than waiting for complaints, MachineSense’s in-cab display proactively alerts operators if they use machines outside of approved time windows or activate restricted functions, like vibratory rolling, ensuring compliance before issues arise.
MachineSense provides verifiable proof of task completion, such as dust suppression or road sweeping, helping to avoid hefty fines by ensuring that compliance requirements are met and documented in real-time.
MachineSense alerts operators when machines exceed site speed limits, helping to maintain safe operation and reduce the risk of accidents.
Ensure machines are only operated in authorised areas, reducing safety risks and improving site compliance with restricted access zones.
MachineSense minimises unnecessary idling, helping to lower fuel usage and reduce operational costs.
By preventing unconscious idling, MachineSense contributes to a cleaner, more sustainable operation, reducing carbon emissions on-site.
Why this works when others don’t
Current solution:
MachineSense:
XXX – Proprietary Data: Different manufacturers use unique data formats, making it difficult for operators to trust the results and for companies to standardise performance tracking.
✓✓✓ – Universal Compatibility: MachineSense works across a wide range of equipment, regardless of the manufacturer or ownership, providing reliable and consistent data across your entire fleet.
XXX – Limited Data Access: Contractors often lack access to data from machines operated by subcontractors or plant hire companies, reducing oversight and control.
✓✓✓ – Automatic Project Allocation: MachineSense automatically assigns machines to the correct projects and tasks, ensuring that the right data is available to the right stakeholders without manual input.
XXX – Poor quality Data: Equipment data is updated infrequently and presented as cumulative performance metrics, making it hard to pinpoint the root causes of issues in real time.
✓✓✓ – Better data: Instead of overwhelming teams with low-quality data, MachineSense focuses on providing actionable insights that help identify the root causes of problems, driving real improvements on-site.
XXX – Data distrust: Without evidence and feedback loops, there is a disconnect with machine operators and data managers.
✓✓✓ – A transparent view: Our built-in camera records short video clips during key events such as speeding or idling, providing evidence that helps validate data and support continuous system improvement.
XXX – Management overload: current solutions require management to delve into data and drive on-site behaviour changes putting extra pressure on existing personnel.
✓✓✓ – Boost operator accountability: Our real-time feedback loop means operators are no longer just passive users of equipment they are actively involved in managing their own compliance, safety, and efficiency. By providing immediate information, MachineSense helps operators make smarter decisions, reducing the need for management intervention
XXX – Delayed data: Data needs analysis and communication, reliance on management to drive change resulting in out of date
✓✓✓ – Live data and events: Data from machines is availible in the cloud in real-time, limits can be set and if they are exceeded a notification can be sent to management, this real-time reporting enables management intervention once risk reaches a certain threashold.
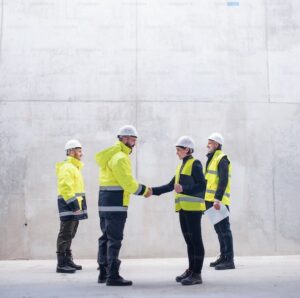
We will work with you!
Collaboration is at the heart of what we do. We don’t just provide sensors and a platform—we help you to make sense of your data, identify risks, and offer tailored solutions based on our extensive industry experience. Together, we’ll ensure you get the most out of your insights, helping you make smarter decisions on site.
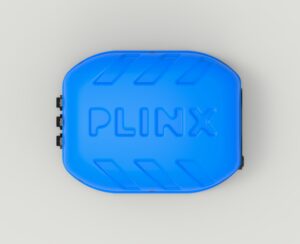
Sensor Features
Intelligent
Each MachineSense unit comes equipped with advanced, in-built intelligence trained from thousands of hours of machine activity. Using its internal sensors, it accurately monitors machine usage without relying on the ECU, offering a seamless, non-invasive solution. Our intelligence models continually evolve, making your equipment smarter over time. Join us on this journey toward continuous improvement.
Retrofittable & Flexible Mounting
Construction equipment varies widely, often with multiple pieces of technology already installed. To provide ultimate flexibility, MachineSense offers a range of mounting attachments that enable quick, easy deployment on any machine, regardless of shape or size. Designed for tough environments, these attachments ensure secure and durable installation in all conditions.
Ruggedised
MachineSense is built to withstand the toughest environments. High-performance sensors are housed in an impact-resistant casing, reinforced with a laser-cut, anti-crush frame made from premium materials. This durable design protects the electronics, ensuring that even after heavy impacts or high-pressure jet washing, MachineSense continues to deliver reliable data.
Complete visibility
Accurate decision-making starts with reliable information. The MachineSense operator interface includes a 1080p camera, which captures high-quality video around the clock, providing visual records of events and preventing disputes. Day or night, you’ll have the data you need to make informed choices on site.
Precise Location, Anywhere
MachineSense delivers high-precision location tracking by combining GNSS, RTK, and Plinx’s patented Beacon-Based Location technology. Whether in open areas or underground tunnels, MachineSense provides real-time location data and accurate zoning to ensure your machines are where they need to be.
Robust Connectivity
Stay connected in even the most challenging environments. MachineSense offers flexible connection options, including public and private 5G networks, Plinx’s proprietary networking technology, and specialised solutions for underground or remote sites. No matter where your equipment is, you’ll have uninterrupted access to your data.
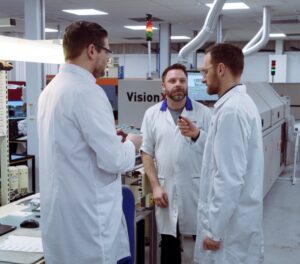
Built proudly In the UK
Every part of the Plinx system is proudly designed, developed, manufactured, and tested in the UK. Our in-house expertise and local supply chain give us the control and flexibility to adapt quickly based on your feedback. We remain committed to working with you to ensure our products and services continue addressing your evolving challenges.
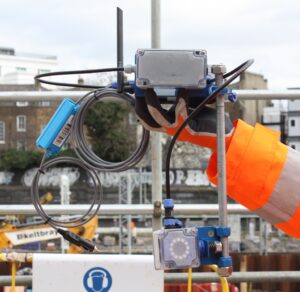
Why Plinx?
In 2020, a valued customer approached us with a challenge: could Plinx technology solve their plant management problems? We were thrilled to say yes. Over the next four years, with input from leading contractors and plant hire companies, we refined MachineSense into the powerful tool it is today. After two years of rigorous testing MachineSense is launched and continues to evolve, with its algorithms adding even more strategic value, revolutionising how our customers manage plant usage on site.